Conduit fittings play a crucial role in industrial electrical systems, ensuring the proper installation and maintenance of electrical conduits. Understanding their importance and following best practices is essential for the safety, efficiency, and functionality of these systems. In this article, we will explore the role of conduit fittings in electrical systems, discuss different types of conduit fittings, examine best practices for their installation, and highlight the importance of maintenance and compliance with industrial standards.
Understanding the Importance of Conduit Fittings
Conduit fittings are integral components in electrical systems, serving multiple purposes. First and foremost, they provide a secure and reliable connection between conduits, allowing for the seamless flow of electricity. Additionally, they offer protection to wires and cables, shielding them from external elements such as moisture, dust, and mechanical damage.
When it comes to electrical installations, the role of electrical wire conduit fittings cannot be overstated. These fittings act as junction points, allowing wires and cables to be connected, branched, or redirected as needed. They facilitate the organization and management of electrical wiring, ensuring a neat and orderly installation. Without conduit fittings, the wiring system would be a chaotic mess, making it difficult to troubleshoot and maintain.
Furthermore, conduit fittings aid in cable pulling, allowing for smooth and efficient routing within conduits. They provide a clear path for cables to pass through, reducing the risk of damage during installation. This is especially important in industrial settings where large quantities of cables are involved. With the help of conduit fittings, cables can be easily pulled through long runs of conduit, ensuring a reliable and efficient electrical system.
See Also: How Electrical Supplies Are Paving the Way for Energy Efficiency
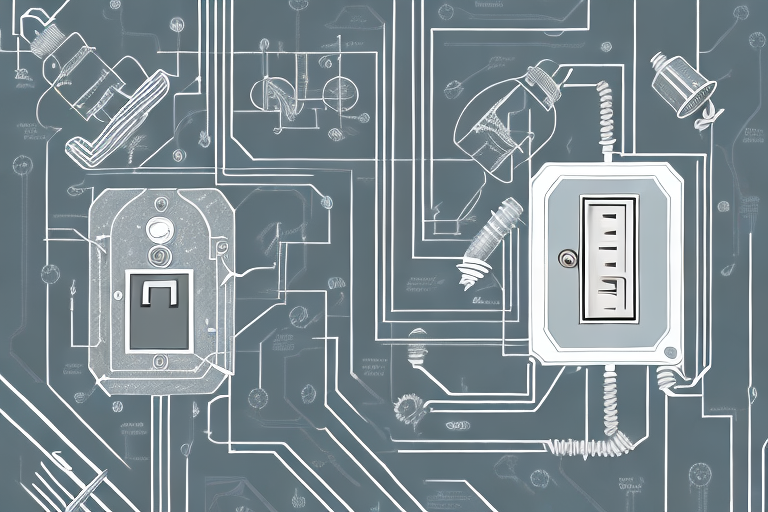
Role of Conduit Fittings in Electrical Systems
Conduit fittings not only provide a means of connecting and organizing electrical wiring, but they also play a crucial role in ensuring the safety of the system. Safety should always be a top priority when working with conduit fittings. Proper grounding and bonding techniques must be followed to minimize the risk of electrical shock or fire hazards.
Grounding is the process of connecting electrical equipment to the earth, providing a path for electrical current to safely dissipate in case of a fault. This helps prevent electrical shock and protects the system from damage. Bonding, on the other hand, involves connecting metal components together to ensure they are at the same electrical potential, reducing the risk of electrical arcing and sparking.
Additionally, it is crucial to use conduit fittings that are suitable for the specific environment and conditions in which they will be installed. Factors such as temperature, chemical exposure, and potential impact should be considered when selecting fittings. For example, in outdoor installations, fittings that are resistant to UV radiation and extreme weather conditions should be used to ensure long-term durability and performance.
Safety Considerations for Conduit Fittings
When working with conduit fittings, it is important to follow industry standards and guidelines to ensure the safety of the electrical system. This includes using fittings that are properly rated for the voltage and current levels of the installation. Using fittings that are not designed for the specific application can lead to overheating, insulation breakdown, and potential fire hazards.
Regular inspections and maintenance of conduit fittings are also essential to ensure their continued effectiveness. Over time, fittings may become loose or corroded, compromising their ability to provide a secure and reliable connection. By regularly inspecting and replacing worn-out fittings, the risk of electrical failures and accidents can be significantly reduced.
In conclusion, conduit fittings are essential components in electrical systems, providing a secure and reliable connection between conduits, protecting wires and cables, and facilitating the organization and management of electrical wiring. They play a crucial role in ensuring the safety and efficiency of electrical installations, and proper selection, installation, and maintenance of conduit fittings are paramount for a successful and reliable electrical system.
Types of Conduit Fittings in Industrial Electrical Systems
When it comes to industrial electrical systems, conduit fittings play a crucial role in ensuring the safety and efficiency of the installation. There are two primary categories of conduit fittings: metallic and non-metallic. Each type offers distinct advantages and is suitable for different applications within industrial electrical systems.
Metallic Conduit Fittings
Metallic conduit fittings, such as threaded connectors, couplings, and elbows, are commonly used in industrial settings. These fittings are known for their exceptional electrical conductivity and mechanical strength, making them ideal for heavy-duty applications. In industrial environments where durability is paramount, metallic fittings are the go-to choice.
Manufactured from materials like steel, aluminum, or brass, metallic conduit fittings are designed to withstand the toughest conditions. Steel fittings, for example, are known for their high tensile strength and resistance to impact, making them suitable for installations in hazardous areas. Aluminum fittings, on the other hand, offer excellent corrosion resistance and are lightweight, making them a popular choice for outdoor applications.
Threaded connectors, one of the most commonly used metallic fittings, provide a secure and reliable connection between conduit sections. Couplings, on the other hand, are used to join two conduit sections together, ensuring a continuous and uninterrupted pathway for electrical wiring. Elbows, available in various angles, allow for smooth directional changes in the conduit system, avoiding sharp bends that could potentially damage the wiring.
Non-Metallic Conduit Fittings
While metallic conduit fittings excel in many industrial applications, there are instances where non-metallic fittings are the preferred choice. Non-metallic conduit fittings, often made of PVC or other durable plastics, offer unique advantages that make them suitable for specific installations.
One of the key benefits of non-metallic conduit fittings is their corrosion resistance. In environments where moisture or chemical exposure is a concern, such as wastewater treatment plants or chemical processing facilities, non-metallic fittings provide long-lasting protection for electrical wiring. The inherent resistance to corrosion ensures that the fittings remain intact and reliable, even in harsh conditions.
Another advantage of non-metallic conduit fittings is their lightweight nature. Compared to their metallic counterparts, non-metallic fittings are significantly lighter, making them easier to handle and install. This feature is particularly beneficial in situations where the conduit system needs to be installed overhead or in areas with limited accessibility.
Furthermore, non-metallic fittings are known for their ease of installation. With their simple push-fit or snap-on mechanisms, these fittings can be quickly and securely connected without the need for specialized tools or extensive training. This not only saves time during the installation process but also reduces the risk of errors or accidents.
Non-metallic conduit fittings are available in various shapes and sizes to accommodate different installation requirements. From straight connectors to adaptors and reducers, these fittings offer flexibility and versatility, ensuring compatibility with a wide range of conduit systems and electrical components.
Whether it’s metallic or non-metallic conduit fittings, the choice ultimately depends on the specific needs of the industrial electrical system. Factors such as the environment, application, and budget should all be considered to ensure the most suitable fittings are selected. By understanding the advantages and characteristics of each type, electrical professionals can make informed decisions that result in safe and efficient installations.
Best Practices for Installing Conduit Fittings
Proper installation of conduit fittings is crucial to ensuring their effectiveness and longevity. Adhering to the following best practices can help achieve optimal results:
Conduit fittings play a vital role in electrical installations, providing a secure and organized pathway for cables and wires. To ensure the smooth operation of the system, it is essential to pay attention to every detail during the installation process.
Proper Sizing and Selection
One of the fundamental aspects of installing conduit fittings is selecting the right size and type. It is essential to choose fittings that match the conduits and cables being used. Fittings that are too small can cause wire damage or overheating, leading to potential hazards. On the other hand, oversized fittings may compromise the integrity of the system, allowing moisture or contaminants to enter. To avoid these issues, it is crucial to consult industry standards and specifications to ensure proper sizing and selection.
Moreover, considering the future expansion of the electrical system is also important. By selecting conduit fittings with extra capacity, you can accommodate additional cables or wires without having to redo the entire installation.
Installation Techniques for Efficiency
When it comes to installing conduit fittings, following recommended techniques is essential to ensure efficiency and reliability. Properly aligning fittings, securely fastening them, and using appropriate tools can make a significant difference in the overall performance of the system.
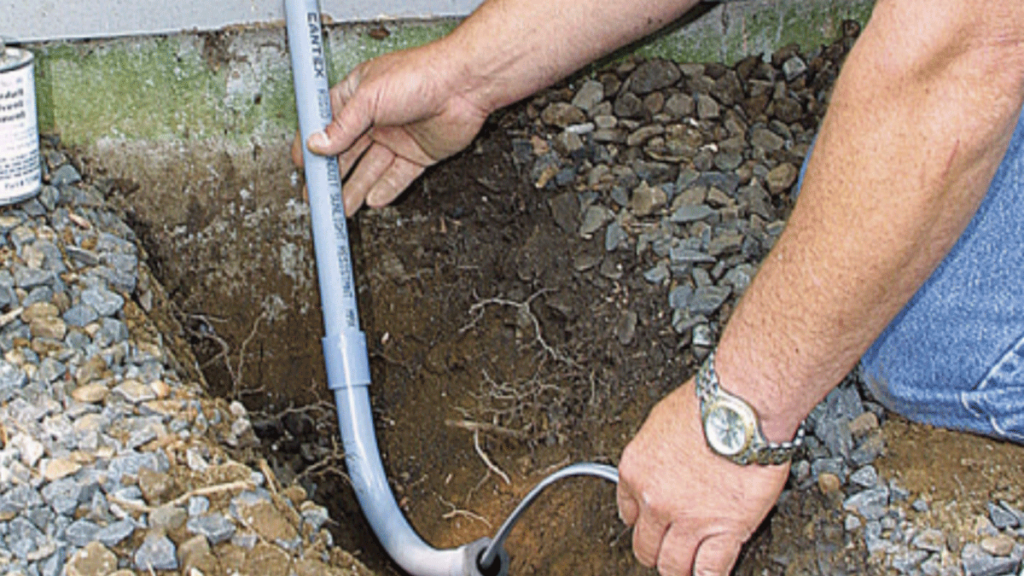
During the installation process, it is crucial to pay attention to the tightness of the fittings. Loose fittings can lead to leaks, causing moisture to enter the conduit and potentially damaging the cables. Therefore, using the appropriate tools, such as wrenches or pliers, to tighten the fittings is crucial.
Another important consideration is the bending radius of the conduit. Improper bending can put excessive stress on the cables, leading to potential damage or even breakage. By following the recommended bending radius, you can ensure that the cables remain intact and maintain their electrical conductivity.
Furthermore, it is essential to inspect the fittings after installation to verify their proper alignment and tightness. This step helps identify any potential issues or areas that require adjustment, ensuring the overall integrity of the system.
By following these best practices, you can ensure the proper installation of conduit fittings, promoting the longevity and effectiveness of your electrical system. Remember, attention to detail and adherence to industry standards are key to achieving optimal results.
Maintenance and Inspection of Conduit Fittings
Maintaining and inspecting conduit fittings on a regular basis helps identify potential issues and prevent malfunctions or failures. Proper maintenance enhances the longevity and performance of the electrical system while minimizing downtime and repair costs.
Routine Inspection Guidelines
Conduct routine visual inspections to check for signs of damage, wear, or corrosion on conduit fittings. Inspect connections to ensure they are tight and properly sealed. Look for indications of overheating, such as discoloration or melted insulation. Any abnormalities should be promptly addressed and repaired.
Maintenance Tips for Longevity
Regularly clean and lubricate conduit fittings to remove dirt, dust, or debris that could impair their functionality. Lubricating fittings with a suitable product can help prevent corrosion and facilitate easier disassembly or reconfiguration if needed. Follow manufacturer recommendations for cleaning agents and lubricants.
Compliance with Industrial Standards
Complying with established industrial standards is vital to ensure the safety, reliability, and quality of electrical systems. Two widely recognized standards in the field of electrical installations are the National Electrical Code (NEC) and the International Electrotechnical Commission (IEC) standards.
National Electrical Code (NEC) Requirements
The NEC provides guidelines for the safe installation of electrical wiring and equipment. Familiarize yourself with the applicable NEC requirements for conduit fittings to ensure compliance. Adhering to these standards helps mitigate risks, protect against electrical hazards, and promote uniformity in installations.
International Electrotechnical Commission (IEC) Standards
The IEC develops international standards for electrical and electronic technologies. Their standards cover various aspects, including conduit fittings. Complying with IEC standards ensures compatibility, safety, and interoperability across global industrial electrical systems.
Conclusion
In summary, proper selection, installation, and maintenance of conduit fittings are essential in industrial electrical systems. Understanding the role and importance of conduit fittings, along with following best practices, helps ensure the safety, efficiency, and compliance of electrical installations. By incorporating these practices and adhering to industry standards, professionals can create reliable and resilient electrical systems that meet the demands of industrial environments.
Leave a Reply